BRAZING WELDING
It is well known that the quality of the welding process is of critical importance for the quality of the starters’ armatures and alternators’ stators.
The goal of this research was to compare the most popular welding methods applied in the welding of stator’s conductor leads and the armature’s commutator.
A comparative study analysing the pros and cons of the TIG (tungsten inert gas welding) and the Brazing Welding methods has been conducted.
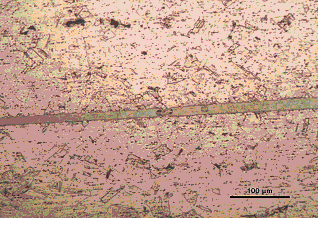
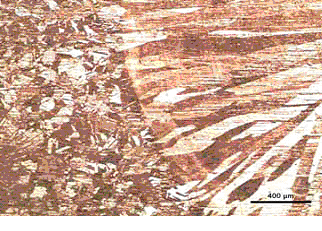
Here are some of the more significant results we obtained:
- The tensile tests demonstrated that the Brazing-welding bond created is 30% stronger than the one realized by TIG welding. The joint obtained by the brazing method is stronger than the base metal.
- The metallographic analysis of the welding spot while employing the brazing method showed that it is solid and without pores or hot cracks. See above metallographic (microscopic) image.
- The TIG welding causes increased porosity of the bond created and as a result the electric resistance is significantly higher, thus rendering the Brazing approach to be the better choice.
- Apart from being more reliable and easily realizable, the Brazing method offers many more advantages when employed for welding of the stator’s conductors ends.
To learn more about this study and its results feel free to contact us, we will gladly discuss our latest advancements in this field and the ways we apply them in our top-notch products.